z racji tego że niektórzy lubią wiedzieć jak coś działa wrzucam artykuł Erica Zapletala, "The Steer-Axis". Myślę że to całkiem ciekawa choć nieprosta lektura.
Written by Erik Zapletal, (C) September 2002.
This article may be freely disseminated, as long as it is not altered from
its present form.
If sections are "cut and paste'd" then the original authorship should be
acknowledged.
~~~~oOo~~~~
THE STEER-AXIS
==============
In previous issues of Racecar Engineering (V11-N6,7,8) we discussed a
steering system's "Ackermann geometry" (which determines the wheel's
steer-angles as they move away from straight-ahead). In those articles we
assumed that the wheels steer around a vertical axis that passes through
the centre of the wheelprint - ie. "centrepoint" steering. However, most
passenger and racecars have a "steer-axis" that is inclined at an angle to
the vertical and intersects the ground at some distance from the wheelprint
centre. This article discusses the geometry of the steer-axis and its
influence on the car's handling and steering feel.
Figure 1:
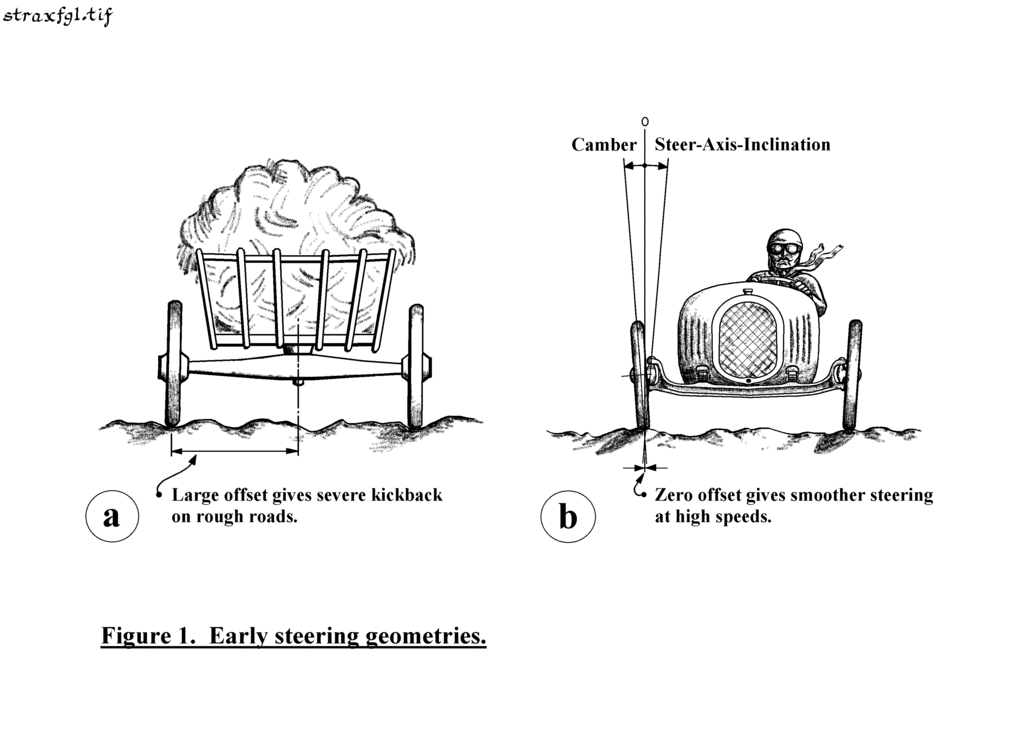
We will start with some history. Early four-wheeled wooden carts had a
front beam-axle with a vertical steer-axis through the centre of the beam -
Figure 1a. The great disadvantage of this system is that any rearward bump
force at one wheel acts on a long lever-arm about the axle's central pivot.
This imposes a large force on the steering linkage that controls the axle,
and ultimately this "kickback" is felt by the horse or driver at the end of
the linkage. In 1817 Rudolph Ackermann promoted the idea (apparently first
developed by Langensperger) of splitting the single beam-axle into two
short half-axles, with each half-axle having its own steer-axis just
inboard of its wheel. This greatly shortened the lever-arm and thus
lessened the kickback from bumps.
The kickback would have been reduced to a minimum if each steer-axis was
placed vertically through the centre of its wheel. However, the wood-spoked
wheels of the time had a bulky, central wheelhub, so each steer-axis was
simply placed as close to its wheel-hub as was practical. These split
steer-axes were further refined by the addition of the "Ackermann" geometry
discussed in the previous articles, although apparently this was only
developed in 1878 by Charles Jeantaud.
The first horseless carriages (1885+) were relatively light and slow, so
the offset steer-axes were acceptable. However, as they became heavier and
faster, steering kickback became a problem again. The wheels were still
either wood-spoked or wire-spoked, so by WWI a common solution to the
kickback problem was to incline both the wheel and the steer-axis so that
the centre of the wheelprint and the ground intersection point of the
steer-axis were brought together, as shown in Figure 1b.
Today, the use of wider tyres has resulted in the wheel being returned to
upright, or leaning slightly inwards on sports and racecars. The use of
dished steel or aluminium wheels allows the steer-axis to be placed
vertically above the centre of the wheelprint - rationally the best
position for minimum steering kickback. However, most modern cars still
have some steer-axis offset, and considerable steer-axis inclination. Why?
Before we can answer this question, we must first look at all the factors
that are relevant to steer-axis geometry.
Figure 2:
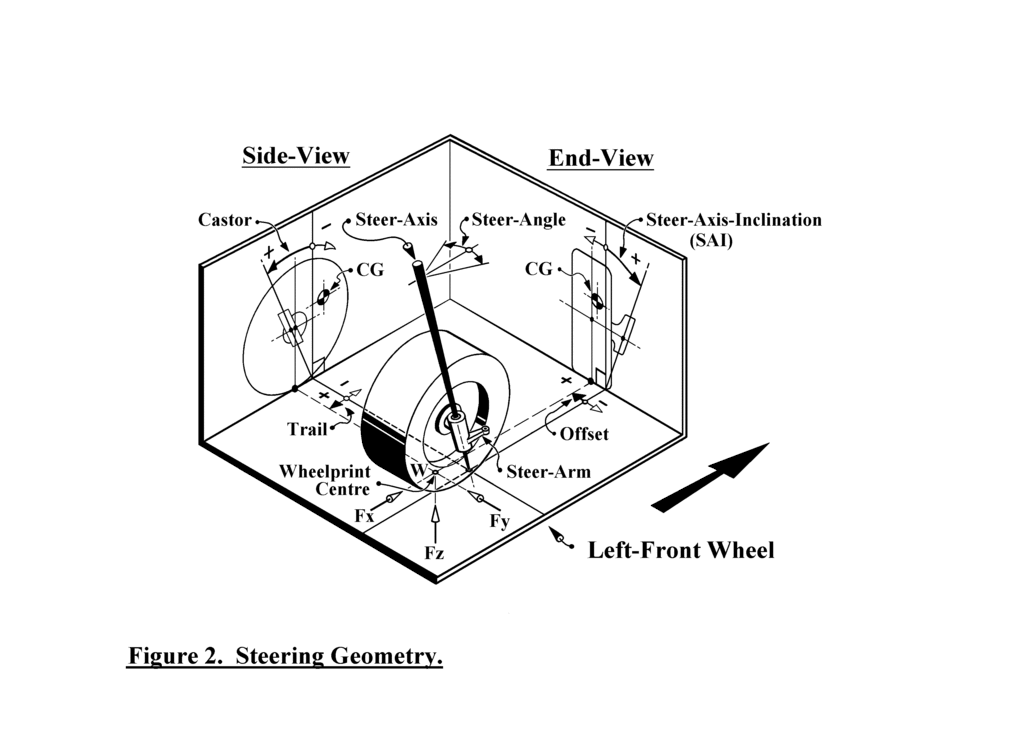
Figure 2 shows the major parameters that we need to consider. A straight
line has four degrees-of-freedom in 3-D space, so we need four parameters
to define the position of the steer-axis relative to the wheel. Here we
locate the ground level intersection point of the steer-axis relative to
the centre of the undistorted wheelprint (point W) using the lateral
"Offset" (sometimes called "scrub-radius") and the longitudinal "Trail"
(sometimes called "castor-offset"). We then define the front-view and
side-view angles of the steer-axis from vertical as the
"Steer-Axis-Inclination" (SAI, sometimes called "king-pin-inclination", or
KPI), and the "Castor" angle (usually called "rake" in the motorcycling
world). The point W is where we consider the resultant force of the
wheelprint's many small distributed forces to act. This resultant force is
usually broken up into its X, Y, and Z components and moments.
If we are designing the "steering-knuckle" (the component that connects the
wheel's axle to the steer-axis and steer-arm) then we must specify some
other dimensions. The "camber" angle is the sideways lean of the wheel from
vertical, usually taken as positive when the top of the wheel leans
outwards from the car's centreline. For simplicity Figure 2 shows a zero
camber angle. The end-view angle between the wheel's axle and the
steer-axis is equal to the SAI plus camber-angle plus 90 degrees. The
"spindle length" (or "pin length") is the end-view distance between the
steer-axis and the central plane of the wheel at axle height (either
measured horizontally, or perpendicularly to the steer-axis). The spindle
length is directly related to the camber, SAI, and Offset dimensions. The
"spindle trail" (or "pin trail", or sometimes "castor-trail"), is the
side-view distance between the steer-axis and the wheel's axle. We must
also specify the position of the steer-arm and any brake mounting brackets.
The steer-arm position relative to the rest of the wheel assembly was
covered in the previous "Ackermann" articles.
As we can see, there are a lot of parameters related to the steer-axis
geometry, and there are even more names and definitions of how to measure
them! There are standards that define the meanings of the various names,
but unfortunately there are too many conflicting standards. Trying to work
out whether "castor-offset" refers to castor, offset, trail, or something
else can be very confusing! Probably the best approach when designing the
front wheel assembly is to communicate via engineering drawings (no names,
just dimensioned pictures). In this article we will refer mainly to the
Offset, Trail, SAI, and Castor, as shown in Figure 2. We capitalise these
specific parameters to avoid confusion.
These four main parameters are not constant. When a car's body rolls or
pitches the SAI and Castor angles change. Depending on the type of
suspension, SAI and Castor can also change when the wheel bounces up or
down relative to the body. When the Castor changes, then the Trail also
changes. During cornering the tyre distorts sideways and the effective
wheelprint centre W moves in the direction of the road-to-tyre forces. This
changes the Offset. If body or suspension movements cause the SAI to
change, then the camber angle also changes relative to the road, and the
wheelprint centre moves towards the more heavily loaded side of the wheel,
again changing the Offset.
Our aim when designing the steering geometry is to minimise kickback when
travelling over rough roads, and at the same time to give the driver a good
feel for the level of front wheel grip during cornering. We also want to
have each front wheel positioned during cornering so that it can deliver
the greatest possible force, with the least amount of wear. Although the
Offset, Trail, SAI and Castor are not constant, we can say that, in
general, the larger the instantaneous Offset and Trail, then the larger the
lever-arm about the steer-axis for the wheelprint forces, and the larger
the potential kickback on rough roads. The larger the instantaneous SAI and
Castor, then the larger the change in camber angle as the wheel is steered
about the steer-axis, and the larger the potential change in wheel grip and
wear rate.
The major external forces acting on a front wheel are the
road-to-wheelprint forces, the driveshaft torque (if the front wheels are
driven), the inertial forces of the wheel assembly's mass, and aerodynamic
forces. Of these, the wheelprint forces are the largest, and the aero
forces are small enough that we won't consider them again. We want the
majority of these forces directed towards the steer-axis, or else balanced
around it. From the steer-axis the forces travel to the chassis via the
suspension control arms. The steering linkage, acting on the steer-arm, has
to provide a moment that counters any imbalance of the forces about the
steer-axis.
If there are any larger than necessary forces acting on the steering
linkage, then we either have to make the entire steering linkage stronger
(and heavier), and possibly add power steering (more weight again), or we
have to accept reduced reliability of both the linkage and the driver.
Since the steering linkage cannot be perfectly rigid, any excessive forces
will cause it to deflect and thus change the wheel's steer-angle. This
happens even if a power steering system prevents the forces getting through
to the driver. The deflected steer-angle changes the wheel's axial (or
"slip-angle") force, which can adversely effect the ride comfort, handling,
and grip level of the car.
We will now consider what happens if we start with the four steer-axis
parameters at zero (ie. a vertical steer-axis through the wheelprint
centre), and then vary only one parameter at a time. In some of the
following equations we use the small angle approximation where we assume
that for an angle A measured in radians; Sin A = Tan A = A, and Cos A = 1.
~o0o~
OFFSET
=======
Typical Offset values range from -5cm (W inboard of the steer-axis) to
about +10cm, although in some cases it is much larger positive.
Any longitudinal Fx force at the wheelprint, acting on the Offset
lever-arm, will exert a torque about the steer-axis. The Offset torque is;
To = Fx x Offset (Nm)
where;
To = torque about the steer-axis due to Offset (Nm).
Fx = longitudinal force at wheelprint centre (N)
Offset measured in metres (m).
ACCELERATION AND BRAKING - We can estimate the maximum size of the
longitudinal Fx force during acceleration (for a front-drive car) or
braking by using the vertical load on the wheel, Fz, multiplied by the
tyre's "Coefficient of Friction" (Cf);
Fx = Fz x Cf (N)
where;
Fz = vertical load on wheel (N).
Cf = tyre coefficient of friction.
The Cf values derived from tests range from 0.1 on ice, to 2.0 for soft
compound racing tyres on coarse tarmac.
Example;
Offset = 0.05m (5cm)
Cf = 1.0 (typical of a good tyre on a dry sealed road)
then;
To = Fz x Cf x Offset
= Fz x 1.0 x 0.05
= Fz x 0.050 (Nm)
This is the torque about the steer-axis just as the wheel starts to spin
during acceleration, or just as it locks up during braking. Note that the
Offset torque is due to the horizontal Fx force. We show it here in terms
of the vertical Fz force so that we can compare it with other torques about
the steer-axis in later sections.
If there is any difference between the grip (ie. Cf value) at the left and
right wheels, then the left and right Offset torques will be unbalanced and
the steering will pull to one side. Even if the grip levels are equal the
steering linkage will be stressed by these torques. In the above example,
if the steer-arms are 0.1m long (10cm) then the load on the steering joints
and track rods is 0.5 x Fz, ie. 50% of the vertical load on the wheel.
ROLLING DRAG - When a wheel rolls in a straight line on a smooth road it
has a rearwards rolling drag force that is related to the vertical load Fz
on the wheel;
Fxr = Fz x Cr (N)
where;
Fxr = rolling drag force (N).
Fz = vertical load on wheel (N).
Cr = coefficient of rolling drag.
The coefficient of rolling drag is typically 0.01 (1%) for pneumatic tyres
on sealed roads. As a car corners, the outer tyres become more heavily
loaded than the inner tyres and their rolling drag increases
proportionally. If the front wheels have positive Offset then the increased
drag on the outer wheel, acting on the Offset lever-arm, tries to turn the
front wheels toward straight-ahead. This self-centring torque is sometimes
claimed as an advantage of positive Offset, but its magnitude is actually
very small.
Example;
We assume that the car is cornering hard enough to lift its inside wheel
(so that the outer wheel carries double the normal weight).
Offset = 0.05m (+5cm)
Cr = 0.01
then;
To = Fz x 2 x Cr x Offset
= Fz x 2 x 0.01 x 0.05
= Fz x 0.001 (Nm)
The nett self-centring torque is the difference between the inner and outer
wheel's torques, so if the inner wheel is still on the ground the nett
torque will be less than in the above example. The cornering forces distort
the tyres laterally so that the outer wheel's Offset decreases and the
inner wheel's Offset increases. This further reduces the nett torque.
When driving off-road the rolling drag varies according to the surface. On
some types of dry sand, or wet mud, the coefficient of rolling drag can
increase to about 0.2. Since the left and right wheels are not always on
the same surface, the difference in the rolling drag forces (from 1% to 20%
of Fz) acting on the Offset lever-arms gives an irregular pulling on the
steering.
KICKBACK - The rolling drag figures apply to relatively level surfaces. If
a wheel drops into a pothole, or hits a sharp bump or kerb, then the
resulting rearwards force can be greater than the vertical Fz force.
Example;
Offset = 0.05m (as before)
Fx = 2 x Fz (N) (a very harsh bump)
then;
To = Fz x 0.100 (Nm)
This is a substantial kickback torque!
If the car has wide tyres and the road surface is irregular then
longitudinal forces acting on the edges of the tyres can be passed on to
the steering wheel even if there is zero Offset. However, in general, more
Offset means more steering pull and kickback.
LIGHTER STEERING - An advantage that is claimed for Offset is that it can
make the steering lighter when the car is stationary. The Offset allows the
wheel to roll about the steer-axis as it is steered. This allows new
sections of tyreprint to be set down on the road with less scrubbing than
if the tyreprint rotates about its centre. However, if a car with zero
Offsets is allowed to creep forward at 1 kph (~0.3m/s), and the road wheels
are steered through 30 degrees in one second, then the steering load is the
same as that of a stationary car with 0.6m Offsets. Furthermore, if the
stationary car with 0.6m Offsets has the brakes applied, then it is almost
impossible to steer the wheels! Besides, this lighter steering advantage
only applies when the car is stationary, so it is of little importance to
racecars.
~o0o~
TRAIL
=====
Typical Trail values range from -1cm to +5cm (sometimes up to +10cm).
Any lateral (or "axial") Fy force at the wheelprint, acting on the Trail
lever-arm, will exert a torque about the steer-axis. The Trail torque is;
Tt = Fy x Trail (Nm)
where;
Tt = torque about the steer-axis due to Trail (Nm).
Fy = lateral (axial) force at wheelprint centre (N).
Trail measured in metres (m).
CORNERING - Positive Trail is the main means of providing dynamic
self-centring to the steering. Any change in wheel steer-angle from
straight-ahead leads to an axial Fy cornering force at the wheelprint
centre that pushes the wheelprint back to the straight-ahead position. If
we have a tyre's cornering performance curves then we can read off its
axial Fy force for a particular slip-angle and vertical Fz load, and thus
calculate the self-centring torque. Alternatively, we can make the
following approximation (adequate for our purposes here). We assume that
the axial force rises linearly up to a peak slip-angle, after which it
levels off at a constant peak axial force. Thus;
Fyp- = Fz x Cf x As / Ap (N)
and;
Fyp+ = Fz x Cf (N)
where;
Fyp- = axial force below the peak slip-angle Ap (N).
Fyp+ = axial force above Ap (N).
Fz = vertical load on wheel (N).
Cf = tyre coefficient of friction.
As = slip-angle of tyre (measured in degrees or radians).
Ap = peak slip-angle of tyre (measured in the same units as As).
(Fz x Cf / Ap is the tyre's "cornering stiffness" (N/deg or N/radian))
Example;
Trail = 0.05m
Cf = 1.0
As = 1 degree
Ap = 6 degrees
then;
Tt = Fz x 1.0 x (1 / 6) x 0.05
= Fz x 0.0083 (Nm)
This Trail self-centring torque will rise by the same amount for each extra
degree of slip until the peak slip-angle is reached (ie. the car is
cornering at its limit), after which;
Tt = Fz x 1.0 x 0.05
= Fz x 0.050 (Nm)
The Trail torque is due to the axial Fy force, but as before, we show it in
terms of the vertical Fz force so that we can compare it with the torques
in other sections. Both the front wheels' Trail torques act in the same
direction so they are added together for the nett torque. The Trail
self-centring is thus seen to be much larger than the self-centring due to
Offset and rolling drag given in the previous section.
Figure 3:
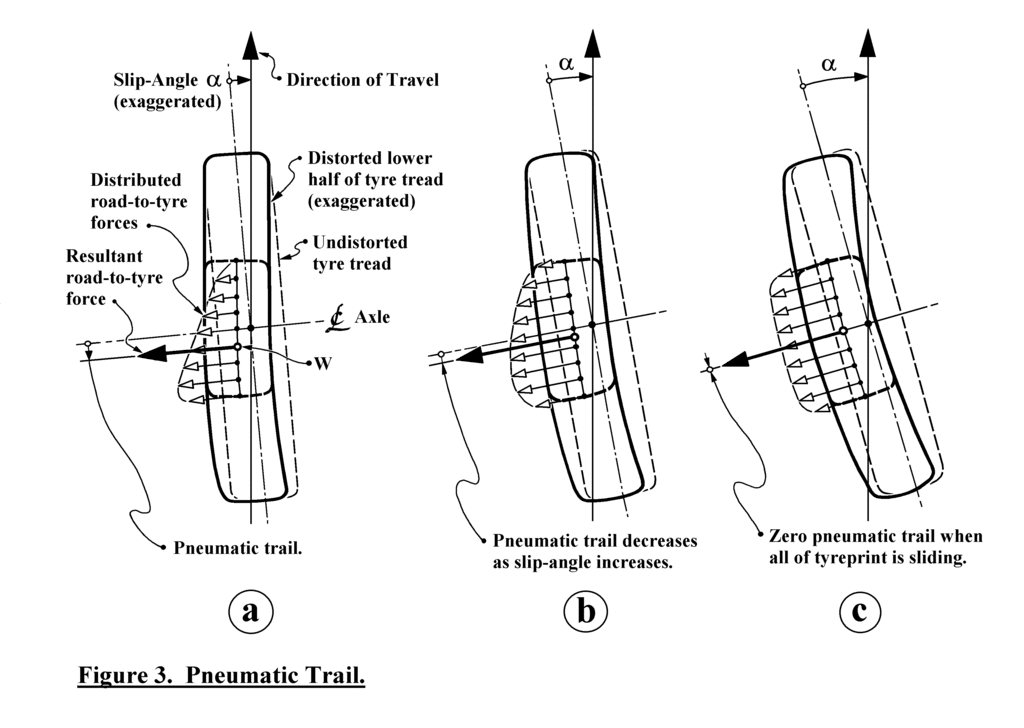
The Trail shown in Figure 2 is the "geometric" Trail (or sometimes
"mechanical" Trail). The geometric Trail is assisted by the "pneumatic
trail" depicted in Figure 3. The forces that build up in the tyreprint
during cornering are initially greatest towards the rear of the tyre. At
low slip-angles (Figure 3a) no part of the tyreprint is sliding on the
road. Rather, the circular hoop of tread is skewed relative to the wheel,
which allows the wheel to "crab" sideways. The forces are due to the
elastic deformation of the tyre - more sideways deflection at the rear of
the tyre, so more force. The vector sum of the distributed tyreprint forces
thus acts behind the centre of the undistorted tyreprint. This distance is
the pneumatic trail. As the cornering force increases the rearmost sections
of the tyreprint reach their friction limit and start to slide (Figure 3b).
These sections of tyreprint are at (or just below) their maximum axial
force, while the forward sections are still increasing in force. Thus the
vector sum of the forces is still increasing, but its point of action is
moving forward. When the tyreprint is fully sliding (Figure 3c) the
distributed tyreprint forces are all equal and the resultant force is
approximately at the wheelprint centre.
The tyre behaviour in Figure 3 can also be presented as an axial force plus
a "tyre self-aligning torque" that both act at the undistorted wheelprint
centre. The tyre self-aligning torque is zero at zero slip-angle (ie. no
axial forces), it grows rapidly at moderate slip-angles as the axial forces
increase at the rear of the wheelprint, then it decreases to zero at larger
slip-angles as the axial forces at the front of the wheelprint catch up to
the forces at the rear of the wheelprint.
Whether we think in terms of pneumatic trail or tyre self-aligning torque,
a pneumatic tyred wheel is self-centring (at low to medium slip-angles)
even if it has zero geometric Trail. The pneumatic trail (or self-aligning
torque) should be included in any calculations of the torque about the
steer-axis. A wheel with tall, narrow tyres has a longer tyreprint, and
consequently a longer pneumatic trail than a wheel with low-profile, wide
tyres. An increase in vertical load or a reduction in tyre pressure also
lengthens the tyreprint, and so also increases the pneumatic trail. At
moderate slip-angles (2 to 4 degrees), where the self-aligning torque is at
its maximum, the pneumatic trail can be as large as 5cm.
The reduction in pneumatic trail as the tyre approaches peak axial force is
one of the main signals to the driver that the front tyres are starting to
slide. We don't have to drive fast to feel this loss of self-centring force
- any slippery road, such as ice or wet clay, makes the steering feel much
lighter. We can adjust the strength of the loss-of-grip signal by varying
the size of the geometric Trail. A small or zero Trail gives light steering
with almost no feel at the limit, while large positive Trail makes the
steering heavy, but less so at the limit.
STRAIGHT RUNNING - Trail can cause a torque to act about the steer-axis
even when the car is driven in a straight line. Since the Trail torque is
created by lateral forces, it is felt whenever there are lateral forces on
the car from sidewinds, or from the gravitational force on the car when it
is being driven on a laterally inclined road. If a car has a lot of Trail
then the steering pulls in the direction of sidewinds (ie. turning the car
downwind), and in the downhill direction on inclined roads. Since this can
be tiring for the driver on long journeys, most passenger cars have Trails
that are less than 1cm.
If a car's suspension is arranged such that the wheelprint moves sideways
as it rises and falls over bumps, then the resulting "lateral scrub" causes
a lateral force to act on the wheelprint, which again causes a Trail torque
to act on the steering linkage. The steering pull from this
lateral-scrub-Trail-torque is minimised on bumpy roads by having a
suspension that gives vertical wheelprint movement. For an independent
suspension this means that the "roll-centre" should be close to ground
level.
~o0o~
STEER-AXIS-INCLINATION
====================
Typical SAI values range from 0 to +15 degrees.
CAMBER CHANGE - If a wheel has positive SAI, as in Figure 2, then as the
wheel steers it gains positive camber - the top of the wheel leans out from
the car's centreline. The change in camber is approximately;
Camber Change = SAI x Steer-Angle x Steer-Angle / 2
(all angles in radians).
Or;
Camber Change = SAI x Steer-Angle x Steer-Angle / 6600
(all angles in degrees).
Example 1;
SAI = 10 degrees
Steer-Angle = 10 degrees
then;
Camber Change = 10 x 10 x 10 / 6600
= 0.15 degrees
Example 2;
SAI = 15 degrees
Steer-Angle = 40 degrees
then;
Camber Change = 15 x 40 x 40 / 6600
= 3.6 degrees
Figure 4:
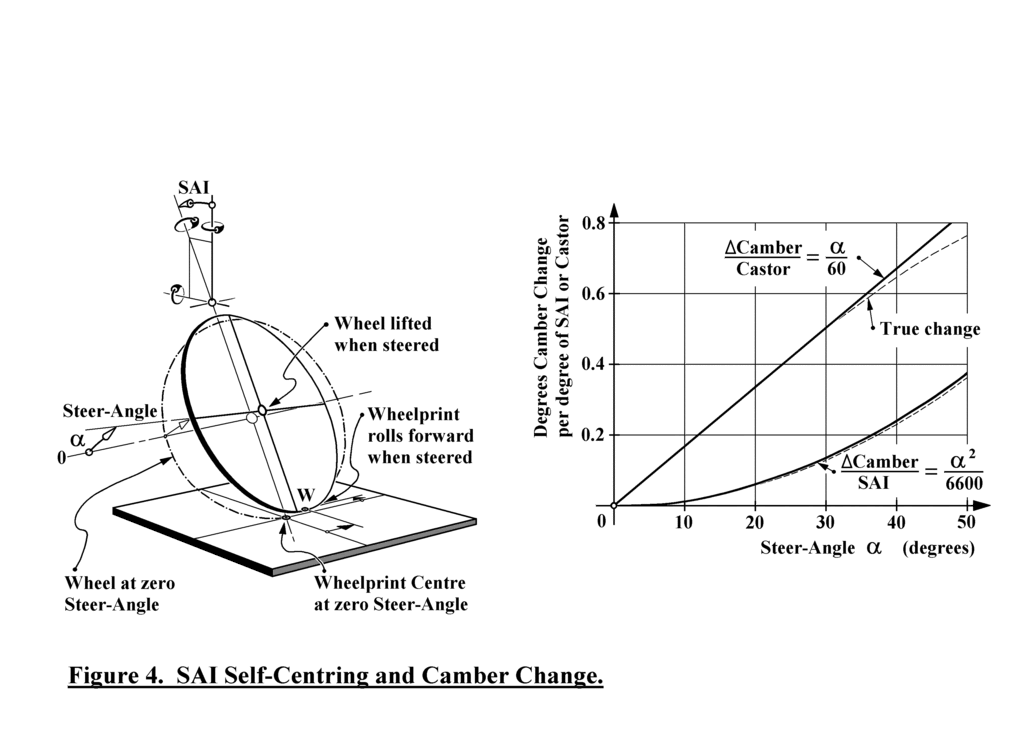
For the range of SAI's and steer-angles on most cars these equations are
accurate to within 10% (see also Figure 4). Generally, for maximum
cornering force we want the wheel to lean slightly into the corner. A car
with positive SAI will corner with the inner wheel leaning into the corner
and the outer wheel leaning out from the corner. Since most of the
cornering force comes from the more heavily loaded outer wheel, a positive
SAI reduces overall grip. A negative SAI leans the outer wheel into the
corner, but, for reasons explained later, very few cars have negative SAI.
SELF-CENTRING - A wheel with SAI (positive or negative) is statically
stable about its steer-axis. That is, a self-centring torque develops
whenever the wheel steers away from straight-ahead. It is sometimes claimed
that the self-centring effect only works if positive SAI is combined with
positive Offset. Others claim that the effect can work with negative
Offset, as long as there is some positive spindle length. However, as shown
in Figure 4, SAI self-centring works even with zero Offset and zero
spindle-length.
As the wheel is steered about its inclined steer-axis it has both vertical
and horizontal components of rotation. The rotation about the vertical axis
gives the change in steer-angle, and the rotation about the horizontal axis
causes the wheel to roll forwards or backwards. The rolling motion causes
the wheelprint centre W and its vertical Fz force to move in front of, or
behind the steer-axis, thus creating the self-centring torque. The torque
doesn't rely on the horizontal Fx or Fy forces so the wheel is
self-centring even when the car is stationary. In effect, the car sits in
its lowest position when the wheel is pointing straight-ahead, and the car
is lifted upwards as the wheel is steered away from straight-ahead.
The SAI self-centring torque is approximately;
Tss = Fz x SAI x SAI x Steer-Angle x Rw (Nm)
where;
Tss = self-centring torque about the steer-axis due to SAI (Nm).
Fz = vertical load on wheel (N).
Rw = radius of the wheel (m).
SAI and Steer-Angle measured in radians.
The self-centring effect of SAI is seen to be directly proportional to the
wheel's radius. This shows that the "flatter" the bottom of the wheel (ie.
the larger the radius), then the greater the stability.
Example;
SAI = 0.17 radians (10 degrees)
Steer-Angle = 0.17 radians (10 degrees)
Rw = 0.3m
then;
Tss = Fz x 0.17 x 0.17 x 0.17 x 0.3
= Fz x 0.0015 (Nm)
This shows that even at quite high steer-angles the SAI self-centring
torque is relatively low compared with the Trail torque.
As seen in Figure 4, when a car with positive SAI's turns a corner the
outer wheel's wheelprint centre (W) moves forward relative to the
steer-axis reducing this heavily loaded wheel's Trail. This may result in
the Trail becoming negative, which leads to a de-centring action - the
wheel turns even more sharply into the corner. The reduction in Trail
during steering is worst for large radius wheels, with large SAI, turning
through large steer-angles. The change in Trail is sometimes explained in
terms of the apparent change in Castor angle (when viewed along the wheel's
axle) that occurs when a wheel with SAI is steered.
LONGITUDINAL WHEELPRINT MOVEMENT - Any forward or rearward movement of the
wheelprint centre allows the vertical Fz force to create a torque about an
inclined steer-axis. This torque is approximately;
Tsx = Fz x SAI x Lwx (Nm)
where;
Tsx = torque about a steer-axis with SAI due to Lwx (Nm).
Fz = vertical load on wheel (N).
Lwx = length of longitudinal (X-axis) movement of wheelprint centre (m).
(Lwx = SAI x Steer-Angle x Rw in the previous section)
SAI measured in radians.
As a car drives over a rough road the bumps first contact the wheels in
front of the axle line, then behind the axle. The bumps thus cause the Fz
force to move forwards and backwards relative to the steer-axis.
Furthermore, the suspension damper causes the Fz force to increase on the
uphill side of the bump, and decrease on the downhill side. The result is a
varying torque about the steer-axis, even though there is no Offset.
Example;
SAI = 0.17 radians (10 degrees)
Lwx = 0.1m (distance of bump (fore or aft) from steer-axis)
then;
Tsx = Fz x 0.17 x 0.1
= Fz x 0.017 (Nm)
Because a wheel with low friction axle bearings cannot exert a torque on
its axle, the horizontal rolling drag force mentioned earlier can only
exist if is accompanied by a forward movement of the vertical Fz force.
This forward movement allows the resultant of the horizontal rolling drag
force and the vertical Fz force to point directly to the wheel's axle,
satisfying the condition of no torque about the axle. The forward movement
of Fz is;
Lwxr = Cr x Rw (m)
where;
Lwxr = forward movement of Fz due to rolling drag force (m).
Cr = coefficient of rolling drag
Rw = radius of the wheel (m).
So the rolling drag force can exert a torque about an inclined steer-axis
even if there is no Offset.
Example;
SAI = 0.17 radians (10 degrees).
Rw = 0.3m
Cr = 0.2 (soft dry sand)
then;
Tsx = Fz x 0.17 x 0.2 x 0.3
= Fz x 0.010 (Nm)
DRIVESHAFT TORQUE - If a wheel of a front-drive car has a steer-axis and a
driveshaft that are not at right angles, then a component of the
driveshaft's torque acts to rotate the wheel assembly about the steer-axis.
This torque is approximately;
Tsd = Td x Asd (Nm)
where;
Tsd = torque component about the steer-axis due to the driveshaft (Nm).
Td = torque from the driveshaft (Nm).
Asd = angle between the driveshaft and the perpendicular to the
steer-axis, measured in radians. If the driveshaft is horizontal then Asd =
SAI.
If, in the extreme, the driveshaft is parallel to the steer-axis then all
of the driveshaft's torque acts about the steer-axis.
Example;
Assume the driveshaft torque is enough to spin the wheel.
Asd = 0.17 radians (10 degrees)
Rw = 0.3m
Cf = 1.0
then;
Td = Fx x Rw
= Fz x Cf x Rw (Nm)
and;
Tsd = Fz x 1.0 x 0.3 x 0.17
= Fz x 0.051 (Nm)
This substantial torque is one part of the "torque-steer" that afflicts
many front-drive cars. If the grip at each front wheel is equal, and the
driveshafts and steer-axes are layed out symmetrically, then the
torque-steer at the two wheels cancels out (although the steering linkage
is still stressed). But if one wheel has more grip than the other and a
limited-slip-differential is used, then the wheel with more grip has more
torque-steer, and the steering pulls to one side (the grippy wheel usually
toe-ins). If the driveshaft-to-steer-axis angles are different, due perhaps
to a transverse engine and different length driveshafts, then the steering
pulls to one side even if the two wheels have equal grip.
The other part of torque-steer is that due to Offset (described earlier). A
positive SAI (with horizontal driveshaft) causes a toe-in torque steer. A
positive Offset also causes toe-in torque-steer. Some of the more powerful
front-drive cars try to cure torque-steer by having a negative Offset that
generates toe-out torque-steer, which is meant to cancel the SAI induced
toe-in torque-steer. The amount of negative Offset required to cancel out
the SAI-torque-steer in the last example is simply 0.051m. That is, for
negligible torque-steer the wheel must have an Offset = -5cm, which makes
the car prone to kickback over bumps.
If the driveshafts are kept perpendicular to the steer-axis (which usually
means SAI close to zero), and zero Offset is used, then neither
SAI-torque-steer nor Offset-torque-steer can develop in the first place.
~o0o~
CASTOR
=======
Typical Castor values range from 0 to +10 degrees.
CAMBER CHANGE - If a wheel has positive Castor, then the top of the wheel
leans into the corner whichever way it is steered. The change in camber is
approximately;
Camber Change = Castor x Steer-Angle
(all angles measured in radians)
Or
Camber Change = Castor x Steer-Angle / 60
(all angles measured in degrees)
Example;
Castor = 6 degrees
Steer-Angle = 10 degrees (ie. a medium corner)
then;
Camber Change = 6 x 10 / 60
= 1.0 degree
Figure 4 shows that Castor has a greater effect on camber than does SAI.
The change in camber that results from positive Castor is beneficial to the
grip of both front wheels during cornering, providing it isn't excessive. A
negative Castor (top of steer-axis leaning forwards) changes the wheel
camber angles in the "wrong" direction during cornering.
SELF-CENTRING - Castor has a self-centring effect that is similar to that
described for SAI. As the wheel is steered away from straight-ahead its
camber angle changes and more weight is carried by one edge of the wheel.
This shifts the wheelprint centre sideways and the offset Fz force then
acts to return the wheel to straight-ahead. As with the SAI self-centring,
this effect is proportional to the Castor and to the radius of curvature of
the tyre, although here it is the curvature of the tyre cross-section that
matters. The self-centring exists even with very narrow tyres, although it
is almost non-existent at small steer-angles. It is greatest on wide, flat
cross-section tyres with stiff sidewalls.
Sometimes people refer to a stabilizing "castor effect" when the effect is
actually due to Trail. This confusion is possibly due to the naming of the
little wheels found under some furniture (eg. office chairs) as "castors".
These castors usually have a lot of Trail, but no Castor angle! Castor by
itself has only a small stabilizing effect, whereas Trail by itself has a
large stabilizing effect. When we increase the Castor on a car's wheel we
usually also increase its Trail, which may also contribute to this
confusion.
LATERAL WHEELPRINT MOVEMENT - Any sideways movement of the wheelprint
centre allows the vertical Fz force to create a torque about a Castored
steer-axis. This torque is approximately;
Tcy = Fz x Castor x Lwy (Nm)
where;
Tcy = torque about a steer-axis with Castor due to Lwy (Nm).
Fz = vertical load on wheel (N).
Lwy = length of lateral (Y-axis) movement of wheelprint centre (m).
Castor measured in radians.
High cornering forces cause a lateral distortion of the tyre that shifts
the wheelprint centre towards the inside of the corner (relative to the
rest of the wheel). The resulting lateral movement of the vertical Fz force
acts to turn the wheel towards straight-ahead.
Example;
Castor = 0.1 radians (6 degrees).
Lwy = 0.05m (5cm - a large value).
then;
Tcy = Fz x 0.1 x 0.05
= Fz x 0.005 (Nm)
If the outer wheel develops significant positive camber during cornering
then the wheelprint centre moves towards the outside of the corner, which
creates a de-centring torque about the steer-axis. The lateral movement of
the wheelprint centre during cornering is greatest with tall, narrow tyres,
and during camber change it is greatest with wide, low-profile tyres. In
both cases the movement can be greater than 5cm, although the resulting
torque is relatively small compared with the Trail self-centring torque.
~o0o~
INTERACTION OF THE PARAMETERS
=============================
When we vary two or more of the steer-axis parameters away from zero, their
interactions can have additional effects to those already mentioned.
SAI + OFFSET - Adding positive Offset to positive SAI increases the
stabilizing effect described in Figure 4. The self-centring torque is
approximately;
Ts+o = Fz x SAI x Steer-Angle x ( SAI x Rw + Offset) (Nm)
where;
Ts+o = self-centring torque due to SAI + Offset (Nm).
Fz = vertical load on wheel (N).
Rw = radius of the wheel (m).
SAI and Steer-Angle measured in radians.
Example;
SAI = 0.17 radians (10 degrees)
Steer-Angle = 0.17 radians (10 degrees)
Rw = 0.3m
Offset = 0.05m
then;
Ts+o = Fz x 0.17 x 0.17 x ( 0.17 x 0.3 + 0.05)
= Fz x 0.003 (Nm)
As with the self-centring due to SAI alone, the total self-centring of SAI
plus Offset is small compared with Trail self-centring. With the addition
of Offset the self-centring effect works even if the wheel has a small
radius. Adding negative Offset to positive SAI can reduce the torque until
it becomes de-centring, but this is not likely in practice.
CASTOR + TRAIL - A narrow wheel with positive Castor and positive Trail is
statically unstable. Any change in steer-angle away from straight-ahead
moves the wheelprint to the side of the steer-axis in plan-view, and the
vertical Fz force acts to increase the steer-angle even further. The car is
lifted to its highest position when the wheel is straight-ahead, and it
drops downwards as the wheel moves away from straight-ahead. The
de-centring torque is approximately;
Tc+t = Fz x Castor x Trail x Steer-Angle (Nm)
where;
Tc+t = de-centring torque due to Castor + Trail (Nm).
Fz = vertical load on wheel (N).
Castor and Steer-Angle measured in radians.
This equation suggests that increasing both Castor and Trail makes the
steering less stable. However, the Castor-plus-Trail instability is swamped
by the extra stability that comes purely from the increased Trail. We can
compare the two torques. At low steer-angles, and assuming that the
steer-angle in the Tc+t equation is the same as the slip-angle (As) in the
Tt equation, we get;
Tt / Tc+t = Cf / (Castor x Ap)
where;
Cf = tyre coefficient of friction
Ap = peak slip-angle of tyre.
Castor and Ap measured in radians.
Example;
Cf = 1.0
Castor = 0.1 radians ( 6 degrees)
Ap = 0.1 radians ( 6 degrees)
then;
Tt / Tc+t = 1.0 / ( 0.1 x 0.1)
= 100
This tells us that the self-centring torque of the axial Fy force on the
Trail lever-arm is 100 times larger than the de-centring torque of the
vertical Fz force on the Castor-plus-Trail lever-arm. If stiffer tyres are
used (smaller Ap) then the ratio of torques is even higher. If wide tyres
are used then the de-centring Tc+t torque probably couldn't arise in the
first place (because of Castor self-centring with wide tyres).
CASTOR + OFFSET - A more powerful interaction is between positive Castor
and positive Offset. (A similar interaction occurs with positive SAI and
positive Trail.) In this case steering the wheels to the left causes the
left wheelprint to be pushed downwards, while the right wheelprint is
lifted upwards. This rolls the body and causes the left-front and
right-rear wheels to carry a greater proportion of the car's weight, while
the other diagonal pair (RF and LR) lose load. The variation in the Fz
loads on the front wheels creates a self-centring effect that is dependent
on the suspension stiffness. The stiffer the suspension springs, then the
greater the variation in loads, and the greater the self-centring torque.
We can use the equation for Castor and lateral wheelprint movement to
estimate the self-centring torque.
Example;
We assume that the suspension and tyres are stiff enough that a steering
movement lifts one front wheel off the ground (so the other wheel is
carrying 2 x Fz).
Castor = 0.1 radians (6 degrees)
Offset = Lwy = 0.05m
then;
Tcy = Fz x 2 x Castor x Offset
= Fz x 2 x 0.1 x 0.05
= Fz x 0.010 (Nm)
Large values of positive-Castor-positive-Offset are common on go-karts.
(These values are much larger than in the above example, but fortunately
for the driver the Fz force is quite small.) Since go-karts have no
differential they are natural understeerers. A locked rear-axle has a
beneficial stabilizing effect on large radius, oval track, Indy type cars,
but it is not at all helpful on tight and twisty go-kart tracks. The large
positive-Castor-positive-Offset steering geometry, combined with the
no-suspension go-kart chassis, lifts the inside rear wheel during
cornering. This not only reduces the inside rear wheel's understeering
thrust, but it also reduces the rear grip via the tyre-load-sensitivity
effect, and moves the handling towards oversteer. While this particular
steering geometry works well for understeering go-karts it is not
recommended for stiffly sprung racecars with open differentials (the inside
rear wheel will spin), or for cars that are already prone to oversteer.
~o0o~
WHEEL INERTIAL FORCES
=====================
The distribution of the wheel assembly's mass, relative to the steer-axis,
has a significant influence on the steering.
LATERAL AND LONGITUDINAL INERTIAL FORCES - During cornering there are
centrifugal forces acting on both front wheels and on the steering linkage.
If the wheel and steering linkage centre-of-gravity's (CG's) are in front
of the steer-axis, due to say, heavy front-mounted brake calipers and
front-mounted steer-arms and rack-and-pinion, then the centrifugal forces
act to turn the steering towards straight-ahead - there is an increased
self-centring effect. With the CG's behind the steer-axis there is a
de-centring effect. Brake calipers are often mounted behind the wheel axle
to minimise the load on the wheel bearings during braking. The de-centring
effect of rear mounted calipers can be countered by the self-centring
effect of a front mounted steering linkage. We can estimate the size of
these torques;
Tcg = Fcg x Lcg (Nm)
where;
Tcg = torque about the steer-axis due to the inertial (centrifugal)
force of the wheel assembly's (and steering linkage's) CG (Nm).
Fcg = inertial force at the CG (N).
Lcg = length of the CG lever-arm (ie. shortest distance from the Fcg
force line to the steer-axis) (m).
Example;
We assume that the wheel assembly mass is one fifth of the quarter-car
mass that it is carrying (ie. unsprung to sprung-mass ratio = 1/5), and the
car is cornering at 1G;
Fcg = Fz x 0.2 (N)
Lcg = 0.05m (5cm - a heavy caliper and steering linkage would be
required for this amount of longitudinal CG offset).
then;
Tcg = Fz x 0.2 x 0.05
= Fz x 0.010 (Nm)
This torque is comparable in size to the self-centring torques given in
other sections, thus the longitudinal position of the wheel CG can be used
to adjust the steering feel.
The position of the wheel's CG has a stronger effect on bumpy roads. Many
suspensions have laterally oriented control arms that cause the wheel to
move sideways as the arms travel through their arcs. These lateral
accelerations of the wheel on bumpy roads result in lateral inertial forces
acting at the wheel's CG. If the wheel's CG is behind or in front of the
steer-axis, then on bumpy roads the lateral inertial forces will create
kickback torques about the steer-axis.
Similarly, if a suspension causes its wheel to move forwards and backwards
as it rides over bumps, then its CG is subject to longitudinal
accelerations and forces. The VW Beetle twin-trailing-arm suspension,
common on many off-road racers, has this property. If the wheel's CG is
offset laterally from the steer-axis, as in the end-view of Figure 2, then
the longitudinal inertial forces again create kickback torques about the
steer-axis. If the steer-axis has significant SAI or Castor angles, then
even a purely vertical inertial force acting on the wheel has a component
that creates a torque about the steer-axis.
Example;
We consider the longitudinal wheel movement of a twin-trailing-arm type
suspension. If the wheel is moving at 45 degrees to the vertical (possible
with short trailing-arms), and the wheel is being accelerated upwards by a
bump, or downwards by the suspension springs, then the longitudinal
inertial force on the CG is one half of the vertical (bump or spring) force
acting on the wheel. So we can assume;
Fcg = Fz x 0.5 (the accelerations during bump can be greater)
Lcg = 0.1m (10cm - can be greater if there is significant Offset and
SAI)
then;
Tcg = Fz x 0.5 x 0.100
= Fz x 0.050 (Nm)
This is another substantial kickback torque that is felt on rough roads.
The direction of the torque changes as the wheel is alternately accelerated
up and down. This results in a wheel "flutter" that is especially obvious
if there is any freeplay in the steering or suspension joints.
If the wheel's CG is coincident with the steer-axis, then neither lateral
nor longitudinal forces acting at the CG can be passed on to the steering
linkage.
GYROSCOPIC FORCES - If we change the camber angle of a rotating wheel we
feel a gyroscopic reaction torque about the wheel's steer-axis. Thus any
suspension that causes camber change with wheel bump will give gyroscopic
kickback on rough roads. The magnitude of the gyroscopic torque is
approximately;
Tgz = Iy x Wy x Wx (Nm)
where;
Tgz = gyroscopic torque about the steer-axis (ie. about the Z-axis) (Nm).
Iy = mass-moment-of-inertia of the wheel about its axle (ie. about the
Y-axis) (kg.m.m).
Wy = angular velocity of the wheel about the Y-axis (radians/sec).
Wx = angular velocity of the wheel about the X-axis (ie. the rate of
camber change) (radians/sec).
The direction of the torque is determined by the direction of the two
angular velocities. Typically, the wheel toes-in as it bounces up and it
toes-out on the way down. If a beam-axle is used then both front wheels
have the same camber change during single wheel bump and the kickback is
doubled. We calculate the torque using;
Iy = Mw x Rg x Rg
where;
Mw = mass of the wheel (Kg)
Rg = radius of gyration of the wheel (ie. radius at which the mass is
considered to act) (m)
Wy = Vx / Rw
where;
Vx = forward velocity of the car (m/s)
Rw = radius of the wheel (m)
Wx = Vz / Ry
where;
Vz = vertical velocity of the wheel during bump or rebound (m/s)
Ry = radius of the "front-view-swing-arm" that determines the
suspension's camber change properties (m).
Example;
We assume that the rotating wheel mass is one tenth of its quarter-car
mass;
Mw = 0.1 x Fz / G (G = acceleration due to gravity = 9.8 m/s.s)
= Fz x 0.01 kg (eg. if Fz = 2kN, then Mw = 20kg)
Rg = 0.2m
Rw = 0.3m
Ry = 2m (typical for a non-parallel double-wishbone suspension)
Vx = 30m/s (108kph)
Vz = 2m/s (vertical bump velocities can approach 5m/s on rally cars, and
10m/s on desert racers).
then;
Iy = Fz x 0.01 x 0.2 x 0.2
= Fz x 0.0004 (kg.m.m)
Wy = 30 / 0.3
= 100 (radians/sec)
Wx = 2 / 2
= 1 (radians/sec)
so;
Tgz = Fz x 0.0004 x 100 x 1
= Fz x 0.040 (Nm)
This gyroscopic kickback is greater with heavier wheels, higher vehicle
speeds, and higher vertical bump velocities - all common on desert racers.
With realistic values for a desert racer the gyroscopic Tgz torque can be
more than ten times greater than the above example. The gyroscopic kickback
is minimised by using a suspension that gives no camber change with wheel
bounce, for example, equal-length-parallel-wishbones, or twin-trailing-arm
type suspensions - again common on desert racers.
For completeness we should add that when the driver steers the front wheels
to the left there is a gyroscopic reaction torque that acts to change the
camber of the wheels, tilting the wheels to the right. Since it is possible
to steer the wheels at 1 rad/sec, the magnitude of the torque is comparable
to that in the previous example. This torque adds to the roll moment on the
car from the cornering forces, but it is relatively small and it only
exists while the wheels are being steered (ie. very briefly for quick
steering movements).
~o0o~
RECOMMENDED GEOMETRY
========================
The above analysis would suggest that if we are designing a steering
geometry from scratch, and if we have no specific reasons for unusual
geometries like that of the go-kart, then we should use the following;
Offset = Zero. For minimal kickback and steering pull on rough roads.
Trail = 0 to +5cm. For dynamic stability (amount depends on driver feel).
SAI = Zero. A laterally inclined steer-axis has few advantages, and many
disadvantages.
Castor = 0 to +10 degrees. For beneficial camber change and a self-centring
effect on wide tyres.
Wheel CG position = on the steer-axis. For minimal inertial kickback.
(And if we are expecting bumpy roads, then we should also use a suspension
that gives vertical wheelprint movement with no camber change.)
So why is it that most passenger and racecars still have positive Offset
and SAI? It seems that the most likely reason is that it is simply easier
to design the wheel assembly that way. Even with modern pressed steel or
aluminium wheels it is easier to package the wheel-hub and disc brake
inside the wheel and then mount the steer-axis at the side of the assembly.
The advantages that are often claimed of positive Offset and SAI, namely
lighter steering, better stability, and better feel, seem to be little more
than excuses for taking the easy option during the design phase.
If positive Offset and SAI really are an advantage, then not having them
should be a disadvantage - a centrepoint steering geometry should not work
well. While not many racecars have used centrepoint steering there is some
evidence to suggest that it does work well. All Citroen models from the
first "DS" introduced in 1955, until Citroen's absorption into Peugeot in
1974, have centrepoint steering (with about +1 degree Castor and +0.5cm
Trail). Although often thought of as eccentric, luxury cars with
underpowered engines, these Citroens excelled in many ice and snow covered
tarmac rallies in Europe, and in the toughest off-road endurance rallies in
Africa through the late 1950's, 60's, and '70's. Their steering geometry
isn't the only reason they did well, but it certainly didn't hurt them.
These front-drive cars have negligible torque-steer, and they track
straight under heavy braking on rough roads, even hands-off the wheel. The
feedback from the steering is lighter than most cars, but it is against a
background of much less noise. All the bumps and the level of road grip can
be felt, but only a very light grip of the steering wheel is required.
Figure 5:
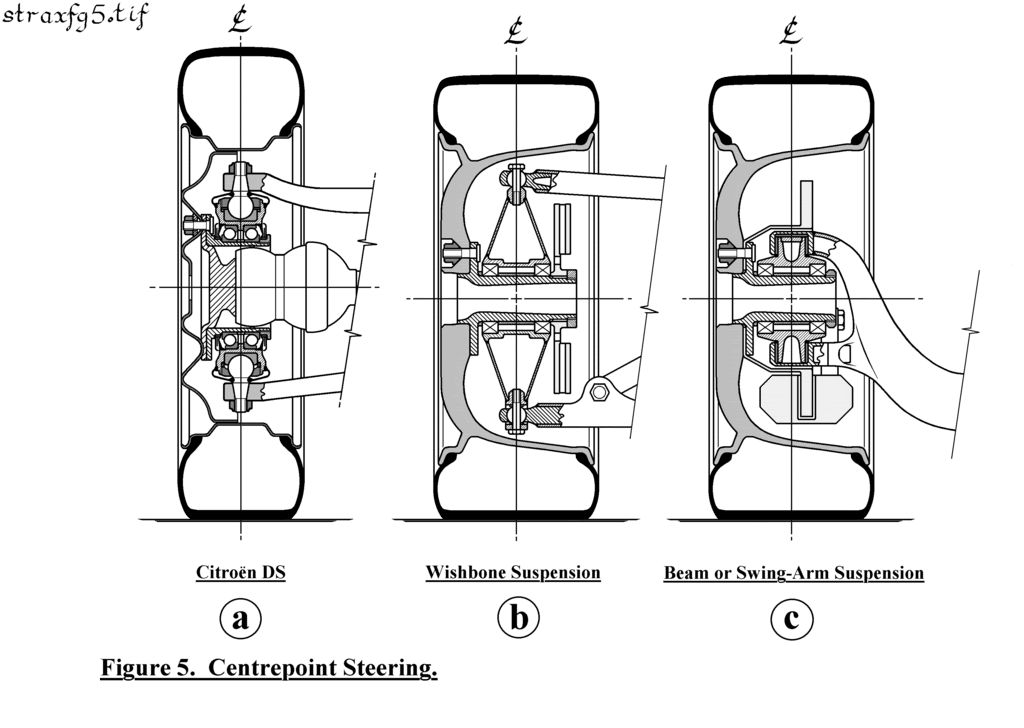
Figure 5a is a cross section of the Citroen DS front wheel assembly, with
its central, vertical steer-axis. The DS can use this simple design because
it has inboard front disc brakes. Mounting the brake within the wheel makes
it harder to achieve centrepoint steering. BMW, Mercedes-Benz, and VW/Audi
use an approach that is somewhat more complicated than Citroen's. They
replace the conventional triangular wishbone with a pair of ball-ended
links that converge on the steering-knuckle. The extension of the link
centrelines forms a virtual pivot-point within the wheel-hub that is close
to the wheel's central plane, thus minimising Offset and SAI. This
multi-link system can replace both wishbones or just the bottom one. By
having an arm that rises up from the steering-knuckle to above the wheel,
the top wishbone can have a single ball-joint directly above the top-centre
of the wheel. Figure 5b depicts another possible approach suitable for a
road racer with low ground clearance, low profile tyres, and
double-wishbone suspension. Figure 5c depicts yet another approach, this
time suitable for a beam-axle or swing-arm suspension.
If it is not possible to achieve a centrepoint design, and if we are
expecting to race over bumpy roads, then we should at least try to minimise
Offset. We can start by pushing the brake disc and wheel-hub deep into the
wheel assembly. If we still have too much Offset, then we can add SAI to
reduce the Offset. If the increased SAI has too adverse an effect on
camber, then we can compensate by adding Castor. If the additional Castor
adds too much Trail, making the steering too heavy, then we have to move
the steer-axis backwards, behind the wheel's axle, to reduce the Trail.
While this rather complicated geometry (similar to Figure 2, and typical of
many cars today) might be acceptable in most conditions, it is not
necessarily a design we should aim for. The simpler centrepoint geometry is
probably better.
~~~~oOo~~~~